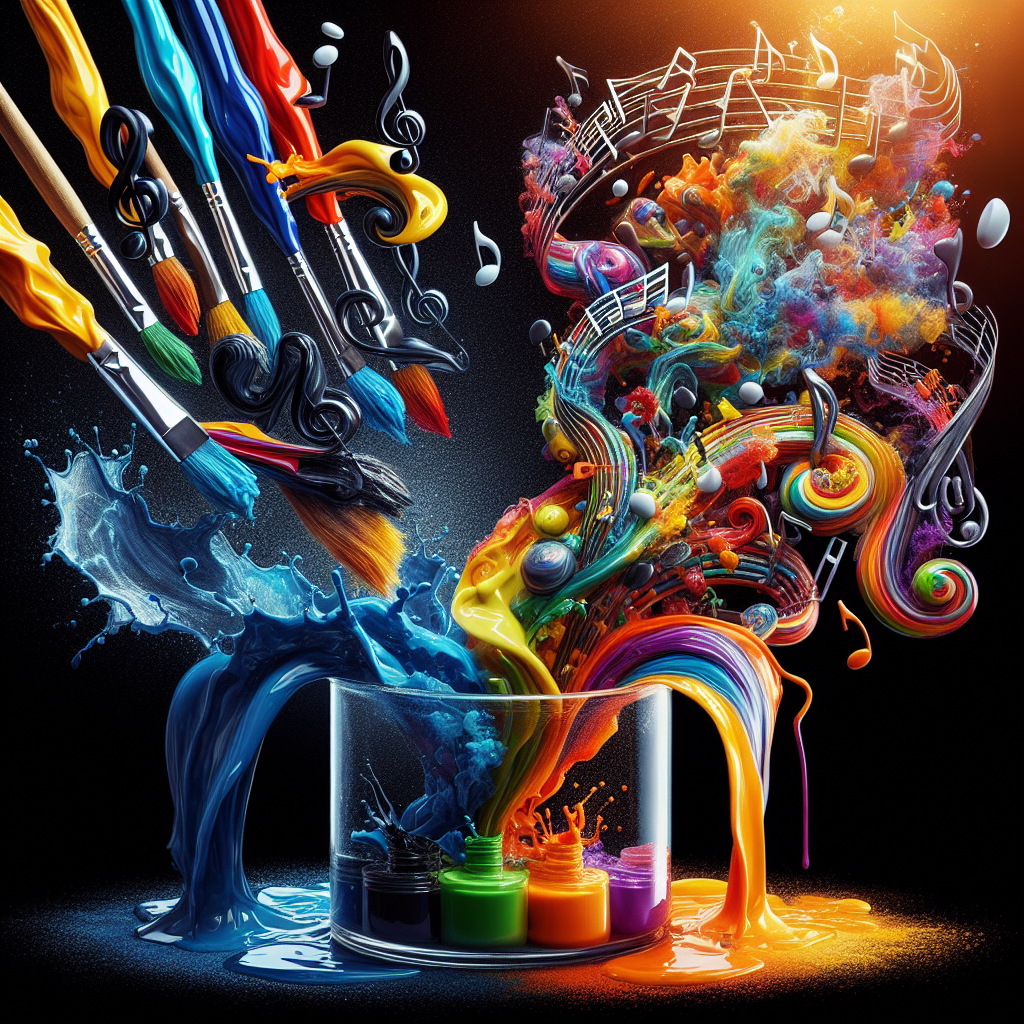
Imagine a world where you can effortlessly combine various elements to create something entirely new and exciting. This is the essence of “How Mix” – an innovative platform that allows you to explore the endless possibilities of mixing different ingredients, ideas, and experiences. Whether you’re looking to experiment with new flavors in the kitchen or blend different art forms together, “How Mix” empowers you to unleash your creativity and discover the magic that happens when diverse elements come together harmoniously. With “How Mix,” the only limit is your imagination. Let’s embark on a journey of endless combinations and delightful surprises!
What is a Mix?
Definition
A mix is the combination of two or more substances or ingredients to create a homogeneous mixture. It is a fundamental process used in various industries to achieve desired results. Mixing involves blending, dispersing, or emulsifying different components to create a uniform mixture.
Importance
Mixing plays a crucial role in many industries as it allows the creation of products with consistent quality and desirable properties. It ensures uniform distribution of ingredients, enhances product performance, and facilitates the reaction of substances. Proper mixing techniques are essential for achieving the desired texture, color, flavor, and overall product quality.
Types of Mixes
There are several types of mixes, each suited for specific applications:
-
Mechanical Mixes: These mixes involve physical agitation or blending, such as stirring, shaking, or mechanical stirring. Mechanical mixes are commonly used in food processing, pharmaceuticals, and chemical industries.
-
Chemical Mixes: Chemical mixing involves reactions between different substances to form new compounds. It is commonly used in the production of drugs, fertilizers, and explosives.
-
Liquid-Liquid Mixes: This type of mix involves combining two or more liquids to form a homogeneous solution or emulsion. Examples include oil and vinegar dressing, milk, and liquid soaps.
-
Solid-Liquid Mixes: Solid and liquid mixing occurs when a solid substance is dissolved or dispersed in a liquid medium. Examples include sugar dissolving in water or adding flour to make a batter.
-
Gas-Liquid Mixes: Gas and liquid mixing is common in various industries, such as the carbonation of beverages or the aeration of dough in baking.
Understanding Mixing Techniques
Basic Principles
Successful mixing relies on understanding and applying certain basic principles:
-
Agitation: Proper agitation ensures the thorough mixing of ingredients. This can be achieved through stirring, shaking, or utilizing specialized mixing equipment.
-
Shear and Dispersion: Shear forces break down particles and distribute them evenly. Dispersion helps to create a uniform mixture by reducing clumping or aggregation of particles.
-
Time and Speed: The duration and speed of mixing impact the final product quality. Mixing for an appropriate amount of time at the right speed ensures proper blending of ingredients.
Tools and Equipment
Various tools and equipment are used in mixing processes, depending on the industry and specific application:
-
Mixers and Blenders: These machines are designed to agitate, stir, or blend ingredients. Examples include mechanical mixers, planetary mixers, paddle mixers, and ribbon blenders.
-
Stirrers and Shakers: These tools are commonly used in laboratories or small-scale mixing operations. They provide manual agitation and are suitable for small volumes of liquids or solids.
-
High-Shear Mixers and Homogenizers: These specialized equipment are used for emulsifying and dispersing substances with high viscosity or those that do not easily mix.
Process Steps
The mixing process typically involves the following steps:
-
Ingredient Preparation: All ingredients are gathered and prepared according to the recipe or formulation.
-
Mixing Assembly: The ingredients are combined in the appropriate order and sequence.
-
Mixing Action: Agitation or blending is initiated using the selected tools or equipment. Proper speed and time are maintained to achieve the desired mix.
-
Quality Control: The mixed product is tested for consistency, homogeneity, and other specified parameters to ensure compliance with standards.
-
Packaging or Further Processing: Once the desired mix is obtained, it can be packaged for distribution or undergo additional processing steps as required by the industry.
Mixing in Different Industries
Food and Beverage
Mixing is a critical process in the food and beverage industry as it ensures the uniform distribution of ingredients and enhances product consistency. It is used in various applications, such as baking, dairy processing, sauce and dressing production, and beverage manufacturing. Proper mixing techniques help achieve desired textures, flavors, and overall product quality.
Pharmaceuticals
In the pharmaceutical industry, mixing is essential for drug formulation. It involves blending active pharmaceutical ingredients (APIs) with excipients to create a uniform mixture. Accurate mixing ensures consistent dose delivery and optimal drug efficacy. In addition, mixing is used in the production of tablets, capsules, ointments, and suspensions.
Construction
Mixing is a fundamental process in the construction industry, particularly in concrete production. Proper mixing of cement, aggregates, water, and additives is necessary to achieve the desired strength, workability, and durability of concrete. In addition, mixing is involved in the production of asphalt, mortar, and other construction materials.
Chemicals
Mixing plays a crucial role in the chemical industry for various processes, including synthesis, formulation, and production of chemical compounds. It is used to combine different chemicals, create solutions or emulsions, and facilitate reactions. Proper mixing techniques ensure the uniform distribution or dispersion of substances and enhance the efficiency of chemical processes.
Common Mixing Problems and Solutions
Inadequate Mixing
One common mixing problem is inadequate mixing, which can result in uneven distribution of ingredients or incomplete reaction. This can lead to variations in product quality and performance. To address this issue, it is important to optimize mixing parameters such as speed, time, and equipment selection. Increasing agitation intensity, ensuring proper ingredient ratios, and using specialized mixing devices can help achieve thorough and efficient mixing.
Segregation
Segregation occurs when particles or ingredients separate during the mixing process, resulting in uneven distribution or inconsistent product quality. This problem may arise due to differences in particle size, density, or electrostatic properties. To prevent segregation, it is crucial to select appropriate mixing equipment, control mixing parameters, and consider the properties of the ingredients being mixed. Additionally, implementing techniques such as fluidization, controlled flow, or using mixing aids can help minimize segregation.
Agglomeration
Agglomeration refers to the clumping or sticking together of particles during the mixing process. This can adversely affect product quality and performance. To prevent agglomeration, it is important to control moisture levels, particle size, and mixing conditions. Utilizing additives or surfactants that act as anti-agglomerants can also help to disperse particles and promote uniform mixing.
Technological Advances in Mixing
Automated Mixing Systems
Advancements in technology have led to the development of automated mixing systems. These systems utilize computer-controlled processes and sensors to ensure precision and consistency in mixing operations. Automated mixing systems offer benefits such as increased productivity, reduced labor costs, improved quality control, and the ability to handle complex mixing tasks. They are commonly used in large-scale industrial production.
Nanomixing
Nanomixing involves the manipulation and control of materials at the nanoscale level to achieve desired properties or reactions. It has gained significant attention in various fields, including pharmaceuticals, materials science, and electronics. Nanomixing techniques allow for the precise combination of nanoscale particles, leading to enhanced performance, improved drug delivery systems, and the development of advanced materials with unique properties.
Continuous Mixing
Continuous mixing is a technique that involves the continuous flow of materials through a mixing system. Unlike batch mixing, which involves discrete batches, continuous mixing offers advantages such as increased efficiency, reduced processing time, and improved product quality. It is commonly used in industries where a constant supply of mixed product is required, such as food production, chemical manufacturing, and plastics processing.
Safety Precautions for Mixing
Hazardous Materials Handling
When working with hazardous materials, such as chemicals or volatile substances, it is crucial to follow safety protocols. This includes wearing appropriate personal protective equipment (PPE) such as gloves, goggles, and respirators. In addition, proper training on handling and storage procedures for hazardous materials should be provided to personnel involved in mixing operations.
Protective Gear
Even in non-hazardous mixing processes, it is important to wear suitable protective gear to minimize the risk of injuries. This may include gloves, safety glasses, aprons, or other protective clothing depending on the specific mixing task. Protective gear helps prevent contact with chemicals, excessive heat or cold, and physical hazards associated with mixing equipment.
Proper Ventilation
Proper ventilation is critical in mixing environments to prevent the buildup of harmful fumes, gases, or dust. Adequate ventilation systems should be in place to ensure the removal of airborne contaminants. This helps to maintain a safe and healthy working environment for personnel involved in mixing operations.
Effect of Mixing on Material Properties
Homogeneity
One of the primary goals of mixing is to achieve homogeneity in the final product. Homogeneity refers to the uniform distribution of ingredients or particles throughout the mixture. Proper mixing techniques ensure that all components are evenly dispersed, resulting in consistent product quality and performance. Homogeneous mixtures have desirable characteristics such as enhanced stability, improved texture, and consistent flavors or colors.
Particle Size Distribution
Mixing can impact the particle size distribution within a mixture. The size and distribution of particles can affect the physical and chemical properties of the final product. Effective mixing techniques help to break down agglomerates, reduce particle size variations, and create a more uniform distribution. Controlling particle size distribution is crucial in industries such as pharmaceuticals, where it can affect drug dissolution rates, bioavailability, and formulation stability.
Rheological Properties
Mixing can also influence the rheological properties of a mixture, which relate to its flow behavior and viscosity. Proper mixing techniques can help optimize the rheological properties of a product, ensuring it flows smoothly, maintains stability, and has the desired texture or consistency. This is particularly important in industries such as food processing, where rheological properties directly impact product quality and consumer acceptance.
Case Studies on Successful Mixing
Food Product Development
In food product development, mixing is crucial to achieving the desired texture, flavor, and appearance of various food products. For example, the production of sauces and dressings relies heavily on proper mixing techniques to ensure the consistent distribution of ingredients and achieve the desired viscosity. Additionally, in baking, mixing plays a vital role in developing the structure and texture of bread, cakes, and pastries.
Drug Formulation
Mixing is critical in drug formulation to create a uniform mixture of active pharmaceutical ingredients and excipients. Case studies in the pharmaceutical industry have demonstrated the importance of optimizing mixing parameters to ensure consistent drug delivery and efficacy. Proper mixing techniques have been shown to enhance dissolution rates, improve bioavailability, and ensure the uniform distribution of drug particles within dosage forms.
Optimized Concrete Mix
In the construction industry, case studies have illustrated the significance of proper mixing in achieving optimized concrete mixes. The precise combination and homogenous distribution of cement, aggregates, water, and additives are essential for achieving desired strength, workability, and durability of concrete structures. Case studies have highlighted the impact of mixing parameters, such as mixing time, speed, and equipment selection, on the performance and longevity of concrete structures.
Future Trends in Mixing Technology
Smart Mixing Solutions
Advancements in automation, artificial intelligence, and sensors are paving the way for smart mixing solutions. These solutions utilize real-time data and feedback to dynamically adjust mixing parameters and optimize mixing processes. Smart mixing systems offer benefits such as increased efficiency, reduced waste, improved product quality, and the ability to adapt to varying ingredient characteristics.
Predictive Analytics
The integration of predictive analytics in mixing processes allows for the accurate prediction of mixing outcomes based on historical and real-time data. This enables manufacturers to optimize mixing parameters, troubleshoot potential issues, and ensure consistent product quality. Predictive analytics can help identify potential mixing problems or deviations early on, allowing for proactive measures to be taken.
Green Mixing
As sustainability becomes a priority in many industries, the concept of green mixing is gaining traction. Green mixing focuses on reducing energy consumption, minimizing waste, and utilizing eco-friendly materials or processes. This includes the use of energy-efficient mixing equipment, recycling and reusing waste materials, and exploring alternative, environmentally friendly mixing techniques.
Conclusion
Mixing is a fundamental process in various industries, enabling the creation of products with consistent quality and desirable properties. Whether it is in food and beverage production, pharmaceutical formulation, construction, or chemical manufacturing, proper mixing techniques play a vital role. Understanding the basic principles of mixing, utilizing the right tools and equipment, and implementing appropriate safety precautions can help achieve efficient and effective mixing. Technological advances, such as automated systems and nanomixing, are shaping the future of mixing, offering improved control, precision, and sustainability. Continuous improvement in mixing technology and practices will continue to drive innovation and enhance product quality across industries.